Streamline Your Rolling Conveyer Automation Today
Discover our advanced automation solutions designed to enhance efficiency in barrel and cask handling. Explore our innovative products that lead the industry.
Custom Conveyor and Barrel Automation Solutions in Tennessee and Kentucky
We specialize in building robust, adaptable conveyor systems that address the real-world needs of modern industry. From material handling of small parts to barrel automation in Kentucky’s distilleries and growing Tennessee manufacturing hubs, our systems are designed to do more than move products they’re built to optimize workflows, increase reliability, and improve your long-term ROI.
Our custom conveyor solutions are engineered to integrate seamlessly into your existing infrastructure while allowing room for future expansion. Whether you’re moving totes, pallets, barrels, or bulk products, we design conveyor lines and automation systems that prioritize safety, speed, and precision.
With decades of experience in conveyor technology, we help production lines, and assembly facilities, bottlenecks, and boost efficiency. From concept to installation, our team offers comprehensive support, including control integration, workstations, and configuration planning tailored to your operation.
Key Services We Offer
Our services are tailored to streamline your barrel and cask automation processes. We prioritize quality and efficiency to ensure smooth operations and optimal performance in a range of environments.
We offer a range of automation services focused on enhancing your barrel and cask handling processes. Our offerings include installation, maintenance, and tailored consulting to ensure the most effective automation solutions. Our goal is to simplify operations while maintaining high standards of quality and efficiency.
We serve a variety of sectors including breweries, distilleries, and wineries. Our automation solutions are crafted to meet the unique needs of each industry, ensuring safe and efficient handling of barrels and casks throughout the production process.
With years of experience in the automation industry, we have honed our skills to deliver robust and reliable solutions. Our team includes seasoned professionals who understand the nuances of barrel and cask handling, ensuring expert guidance and support throughout your project.
Custom Barrel Conveyors for Distilleries of All Sizes
Our custom barrel conveyor systems are specifically engineered for the distilling industry, where moving full barrels safely and efficiently is critical to production. From micro-distilleries looking for low-maintenance entry systems to high-capacity commercial distilleries handling hundreds of barrels per day, we design barrel conveyor solutions that fit the scale and complexity of your operations.
Each custom barrel conveyor is configured based on barrel weight, spacing, speed requirements, and space constraints. Our team works closely with clients to select the best drive type, whether chain driven rollers or our custom stranded chain conveyor; all engineered for heavy loads.
Scalable Solutions for Micro and Commercial Distilleries
Whether you’re scaling from a small craft operation or upgrading a commercial distillery, we provide conveyor systems that evolve with you. Our modular conveyor designs allow for quick reconfiguration, letting you expand or adapt without major infrastructure changes. As your production capacity grows, we help integrate automated pallet conveyor systems, workstations, and inline quality control zones that improve throughput and reduce labor costs.
Gravity roller conveyor sections can be integrated in slower, low-impact zones, while powered roller conveyors and belt conveyors can handle rapid transport, incline changes, and staging. Our systems are used, with installations designed for maximum uptime, low maintenance, and excellent return on investment.
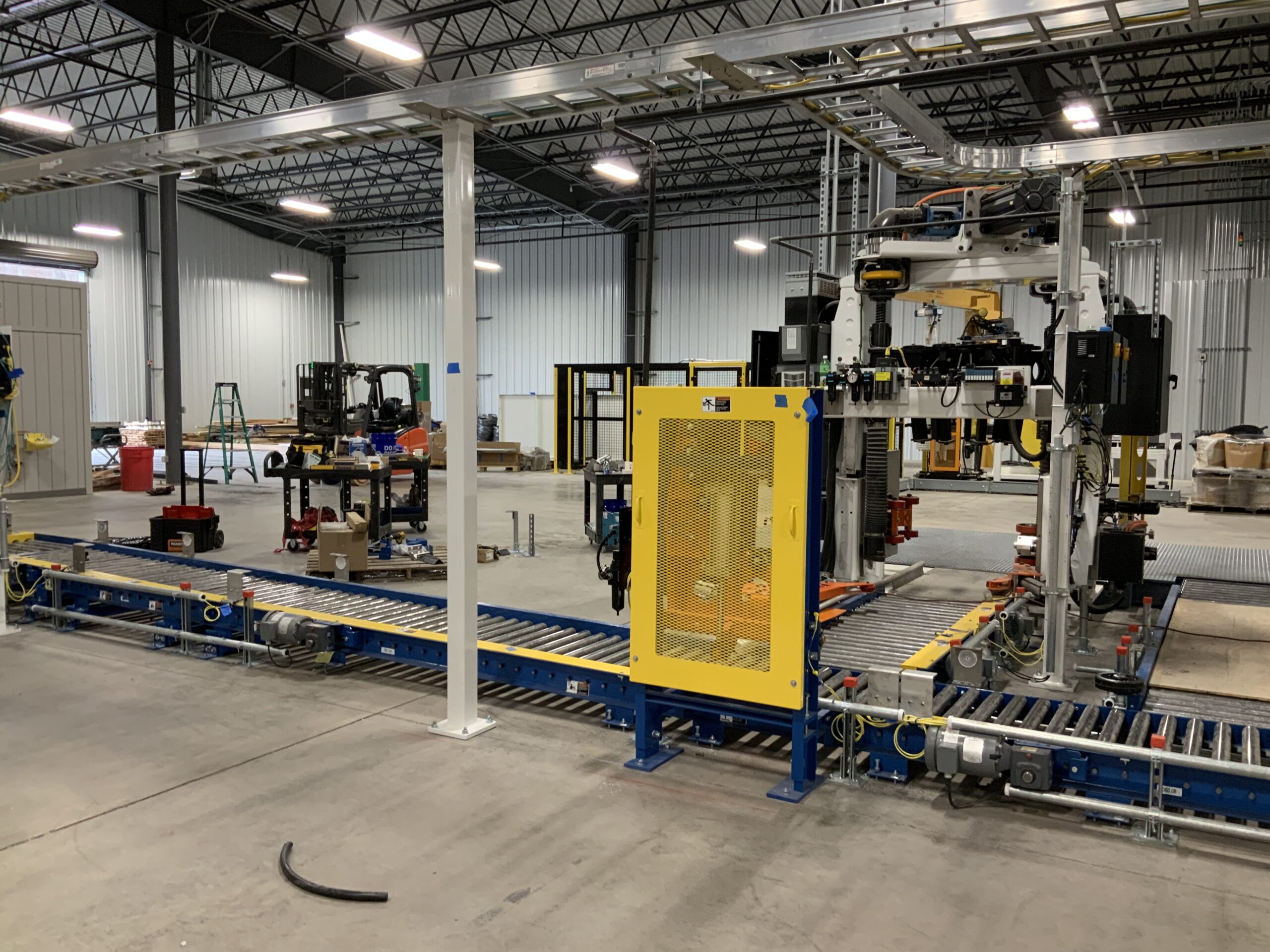
Benefits of Conveyor Automation
Automated rolling conveyors increase efficiency by reducing manual handling. They help streamline operations, minimize errors, and enhance productivity in barrel and cask management.
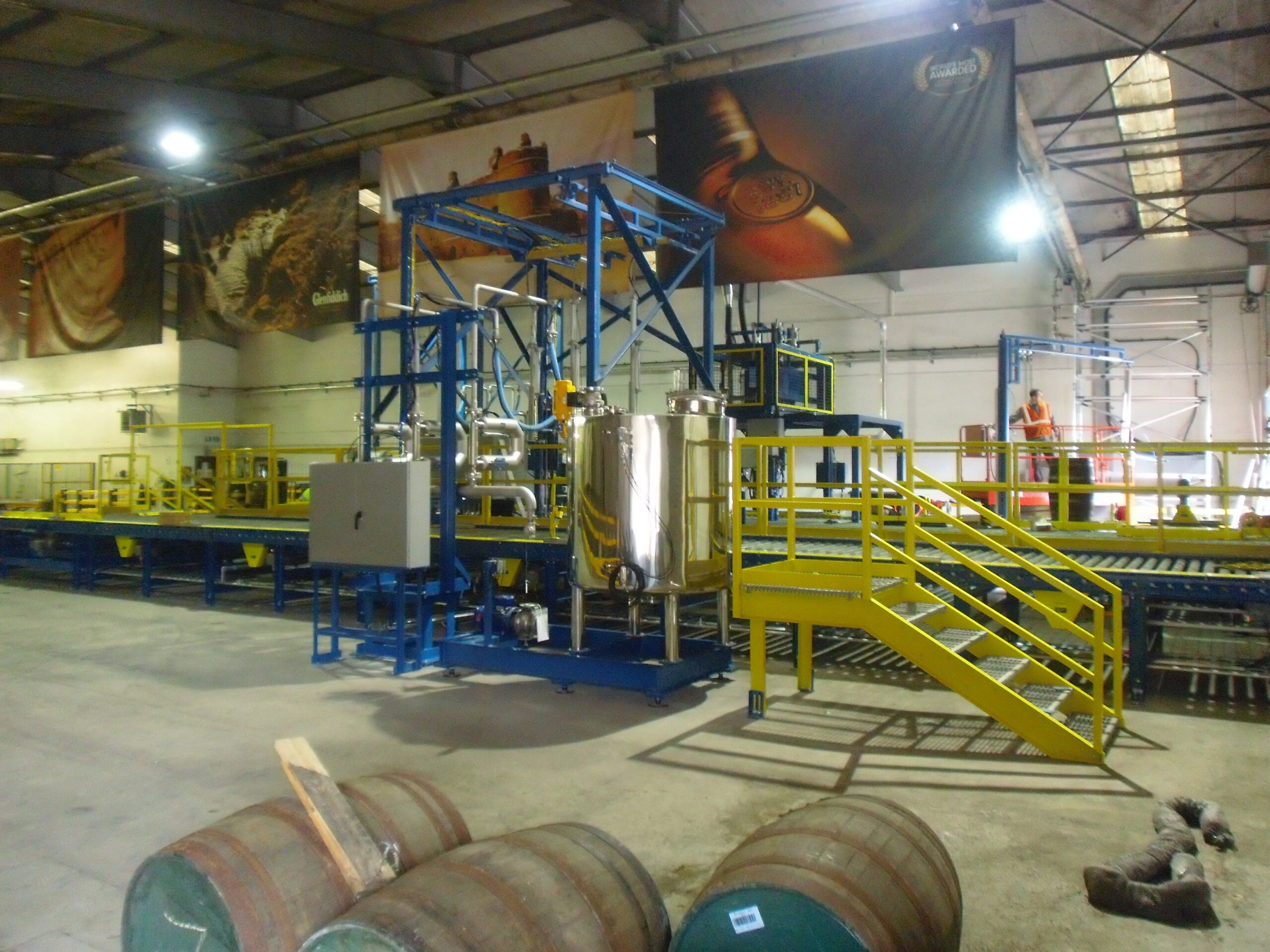
Applications of Our Systems
Our conveyor systems are versatile, suitable for various industries. From breweries to distilleries, they provide effective solutions for filling and moving barrels and casks quickly and safely.
How Do Conveyor Systems Work?
Conveyor systems use mechanical, electrical, or hybrid power to move materials from one location to another within a facility. Depending on the type, such as a belt conveyor, flat top conveyor, or roller conveyor system, they may use belts, rollers, chains, or motor-driven modules to transport goods. The goal is to automate the flow of products and reduce manual handling, resulting in better consistency, increased safety, and higher throughput.
Why Choose Motorized Rollers for Powered Conveyor Systems?
Motorized roller (MDR) conveyors stand out for their energy efficiency, modular design, and precise control. Unlike traditional chain or belt-driven systems, which are better suited for heavy pallets or consistent-speed transport—MDR units power each roller individually. This allows the conveyor to run only where needed, reducing energy use and wear. Their flexible, zone-based control makes them ideal for dynamic environments like Tennessee bottling plants, where safe, efficient automation is essential.
What Is the Most Common Type of Conveyor?
The belt conveyor remains one of the most common conveyor systems due to its versatility. It handles a wide range of materials, from lightweight goods to moderately heavy loads, and it’s ideal for incline/decline transport. For heavier applications like barrel handling or pallet transport, live roller conveyors and chain driven systems are more common, especially in industrial facilities throughout Tennessee.
Automate Your Warehouse Operations to Improve Efficiency and Overall ROI
Automation is the key to better throughput, lower labor costs, and safer handling. By implementing an automated conveyor system, from roller conveyors to smart MDR-based modules, you gain greater control over your process and improve visibility into every stage of production. Whether you’re managing e-commerce fulfillment, distillery operations, or large-scale distribution, our team will help you explore the right solutions.
Advantages of Conveyor Automation
Rolling conveyors enhance workflow by automating complex tasks. They lower the risk of injuries by minimizing heavy lifting, speed up processing times, and foster better inventory management strategies. Reliability and consistency are critical, and our systems deliver that.
Increased Safety
Implementing conveyor automation reduces manual labor, significantly decreasing the chance of workplace injuries and ensuring a safer environment for all employees.
Boosted Efficiency
Our automation solutions allow for seamless operations, improving speed and reducing delays in handling barrels and casks, ultimately optimizing your entire production line.
Our Process Explained
Consultation
We understand your needs and assess your current operations.
Design
Create a tailored plan that best fits your automation goals.
Implementation
Install systems with minimal disruption to your operations.
Support
We provide ongoing maintenance and support for long-term success.
How Conveyor Automation Boosts Production Efficiency
Increased Speed and Output
Automating a rolling conveyor system significantly reduces cycle times, allowing for faster product movement and higher overall throughput.Fewer Manual Steps, Less Labor Dependency
By streamlining repetitive tasks, powered roller and driven roller conveyors reduce the need for manual handling—improving consistency while lowering labor costs.Improved Workflow and Workplace Safety
Conveyor automation minimizes forklift traffic and manual transport, resulting in safer work environments and better operational flow.Adaptable to New Products and Processes
These systems are designed for flexibility, making it easy to switch between product types or workflows with minimal downtime or retooling.Continuous Motion = Continuous Efficiency
Automated conveyors ensure uninterrupted material flow, helping facilities avoid costly stops, delays, or inconsistent output.Minimized Downtime and Bottlenecks
Intelligent material handling reduces points of friction in your process—boosting uptime and keeping your production line moving.Scalable Solutions for Tennessee Manufacturers
Whether you’re a small operation or a large-scale manufacturer, our automation systems grow with your business—supporting long-term scalability across Tennessee and beyond.